Make The Most Of Performance: Proactive Pipeline Welding Inspection Strategies
Important Pipeline Welding Inspection Tips for Quality Control
How can one assure the quality of these welds that link the pipeline areas? By understanding the important pipeline welding examination suggestions, specialists can prevent prospective threats, reduce costly repair services, and promote the integrity of these critical infrastructures.
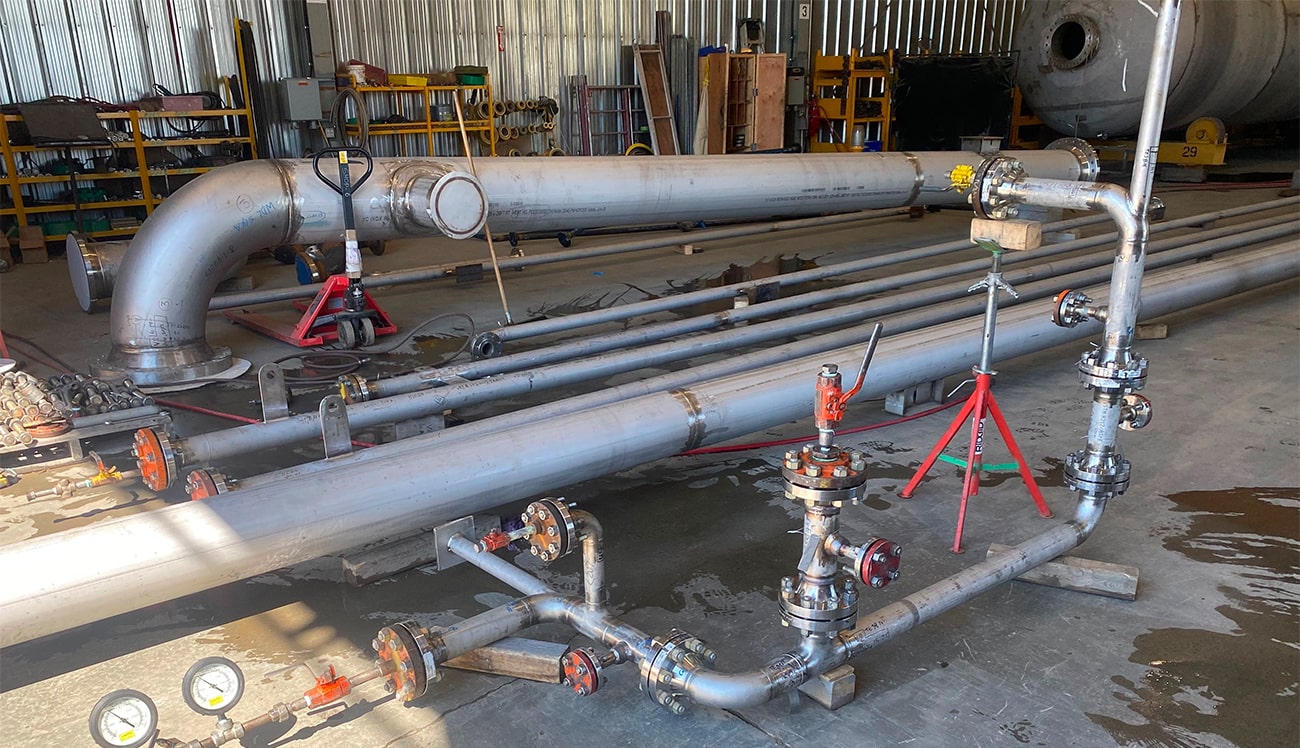
Importance of Welding Examination
Welding assessment plays a crucial duty in making sure the structural integrity and safety and security of pipe systems. By carefully analyzing welds, inspectors can identify any kind of problems or flaws that can compromise the stability of the pipe. These evaluations are important for protecting against leakages, tears, and other potentially devastating failings that can lead to environmental damages, monetary losses, and even death.
The significance of welding assessment can not be overstated, as the top quality of welds directly influences the overall performance and long life of the pipe. Through non-destructive screening methods such as visual assessment, ultrasonic screening, radiography, and magnetic fragment screening, inspectors can identify flaws that might not show up to the nude eye. By recognizing and addressing these concerns at an early stage, welding inspection helps to guarantee that pipes meet sector criteria and governing demands.
Eventually, welding evaluation is a critical facet of quality control in pipe construction, upkeep, and repair (Pipeline Welding Inspection). By maintaining strenuous assessment criteria, market specialists can reduce threats and maintain the security and integrity of pipeline systems
Typical Welding Defects
Amongst the difficulties encountered in pipeline welding, typical flaws can considerably affect the structural stability and performance of the welded joints. Splits in the weld can propagate over time, compromising the architectural honesty of the pipeline. Spotting and attending to these usual issues via extensive examination and quality control processes are vital for making certain the dependability and safety and security of pipe welds.
Inspection Methods for Pipes
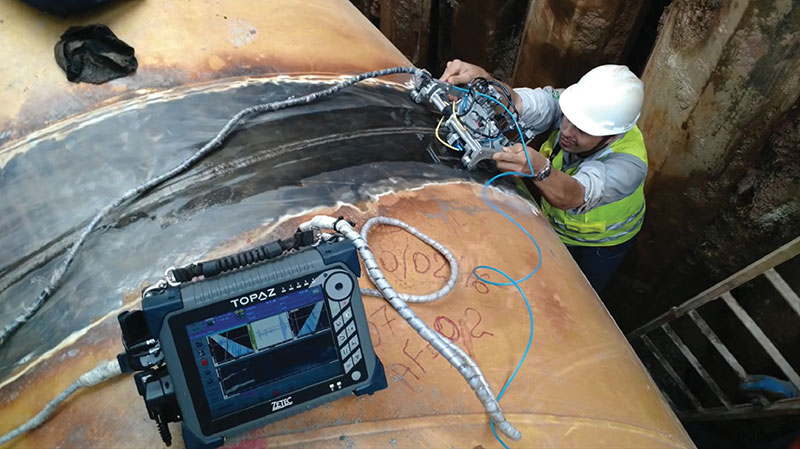

Non-destructive testing (NDT) techniques such as radiographic screening, ultrasonic screening, magnetic fragment screening, and fluid penetrant screening are generally utilized in pipeline welding assessment. Aesthetic evaluation is additionally essential in pipe welding to identify any kind of visible defects or interruptions. In addition, automatic evaluation techniques using sophisticated innovations like drones and find robotics are significantly being used to boost the efficiency and accuracy of pipe assessments.
Making Certain Quality Control Standards
To support strict quality control requirements in pipe construction, thorough adherence to developed sector procedures and standards is essential. Quality control in welding processes calls for a thorough method including different stages of pipe construction. Making sure the top quality of welds entails making use of qualified welders, proper welding procedures, and adherence to sector criteria such as those established by the American Petroleum Institute (API) and the American Culture of Mechanical Engineers (ASME) Inspection and testing play a crucial role in verifying the stability of welds, with strategies like non-destructive testing (NDT) being vital for spotting possible issues. Additionally, maintaining in-depth documentation throughout the welding procedure is crucial for traceability and high quality control purposes. Carrying out a robust quality management system that consists of routine audits and reviews can better improve the overall quality control standards in pipeline welding. By focusing on adherence to these standards, stakeholders can make certain the dependability and safety of pipe systems for the lengthy term.
Avoiding Pricey Repair Services
Provided the vital relevance of preserving stringent quality guarantee standards in her response pipeline building and construction, an aggressive technique to protecting against costly repairs is crucial. Regular upkeep checks and monitoring of ecological aspects that can impact the stability of the pipeline are likewise vital in preventing costly repairs. By investing in preventative steps and prioritizing top quality guarantee at every phase of the pipe welding procedure, business can decrease the risk of expensive repair work and make sure the long-lasting reliability of their facilities.
Conclusion
To conclude, adherence to correct welding evaluation techniques is vital for making sure the quality and honesty of pipelines. By recognizing common welding flaws and applying comprehensive evaluation processes, pricey repair services can be prevented, and quality assurance requirements can be fulfilled - Pipeline Welding Inspection. It is vital for pipeline welders to prioritize assessment treatments to maintain the safety and security and dependability of the infrastructure they are working with
The relevance of welding examination can not be overstated, as the high quality see page of welds straight influences the general performance and long life of the pipeline. Non-destructive testing (NDT) techniques such as radiographic screening, ultrasonic testing, magnetic particle testing, and liquid penetrant screening are generally used in pipeline welding inspection. Visual examination is also vital in pipe welding to identify any visible defects or discontinuities. Additionally, automated evaluation methods utilizing sophisticated technologies like drones and robotics are progressively being utilized to boost the effectiveness and precision of pipeline examinations.In final thought, adherence to correct welding evaluation strategies is necessary for guaranteeing the quality and honesty of pipes.